How To Choose A Leak Testing Method That’s Best For Your Needs
When deciding on the best solution for a leak testing challenge, many factors need to be taken into consideration including the risk, suitability and cost of each method. Various technologies are available and it’s critical to choose one which is optimal to your application requirements
In recent years, huge strides have been made in electronic leak testing methods that use air or tracer gases resulting in new techniques, enhanced sensitivity and faster test cycles. These changes have resulted primarily as a response to cost pressures as well as the need to adapt to a changing environmental and safety regulatory environment.
Air leak testing with micro-flow sensor at pressure conditions.
In this method, the test part is pressurized from a pressure source with the regulator and valve isolating the test part from the source once pressurization is complete. The pressure sensor then monitors and measures the pressurized test part and if the pressure measurement decreases, air is leaking out of the component or assembly under test. As air leaks, the micro flow sensor replenishes the lost air to maintain a constant pressure, with the loss causing an electrical signal which is proportional to volumetric or mass flow. This method has a sensitivity of 5 x 10-4 mbar*l/s.
Air leak testing with mass extraction (vacuum conditions).
This method is an extension of the micro flow sensor one detailed above, and operates on the basic principle of rarefied gas flow. The test is done under a vacuum in order to achieve a higher sensitivity, with sensor designs operating either in a shallow vacuum (continuum/slip flow conditions) or a deeper vacuum (transitional/molecular flow regimes).
This method can be done in a number of ways. The closed container under test can be placed into a vacuum chamber (with a vacuum as low as 1 mbar or less) and the leak rate determined by measuring the remaining flow between the chamber and the vacuum reservoir once the item has been removed. The vacuum can also be applied inside the part under test and the barometric air leaking in can then be measured.
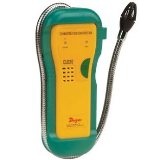
Eight Quick Tips for Electronic Leak Detection
Use Your Detector Second
Before starting to use your detector — stop! Look for signs of leaks and corrosion throughout the entire system. I see many techs who use an electronic leak detector with a very large leak when they would have been better served pressurizing and pinpointing the leak with soap bubbles.
Get a Good Detector
Use a good quality leak detector. Hint: If it costs less than $300, it probably isn’t great. I am fan of the H10G and the H10Pro, although we are testing the Tifzx-1 as a possible option on the recommendation of a few good techs I trust.
Test Your Detector
Check your detector and make sure it actually works every time. The H10G has a reference bottle for testing — use it.
Let the Detector Warm Up
Many leak detectors require a warm up time for the sensor. With the H10G I allow it to run for at least five minutes before I start to use it.
Start Testing at The Top
Most refrigerants are heavier than air. Starting at the top and working your way down will help keep you from picking up a leak below the actual point of origin.
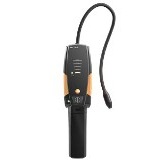
How to Choose and Why Use Leak Detectors?
Refrigerant leak detection
The chart below shows the most common groups of refrigerants we use. With the wide variety of refrigerants now available we have to ensure that the type of leak detector we are using is both suitable and SAFE to use with the refrigerant in the system. Most electronic leak detectors are suitable for CFC, HCFC and HFC’s. Caution should be taken to use suitable electronic leak detectors with HC’s which are flammable. We must not forget soapy water as a very effective leak detector. Many people discount it, but for finding leaks it is possibly the most effective method and lots of people have certainly used it to successfully find some very small leaks.
Corona discharge detectors pull air through an electrical field (corona discharge) around a wire. The presence of refrigerant or other gases in the air changes the current in the wire and triggers an alarm. The problem with this is that it’s not compound specific so any substance the leak detector senses could give false alarms including cleaning chemicals. Not HC suitable!
Heated diode detectors use a heated ceramic diode. The diode generates an electrical current when it comes into contact with halogenated gas which the electronics convert into an alarm. The heated diode sensor is sensitive to contamination, especially from moisture or oil and will need replacement after approximately 100 hours of operation. This type of detector is much less likely to give false alarms and works especially well with R134a. The more expensive models have their own built in sensitivity check mode to ensure the sensing head is actually working. Not HC suitable! This type of leak detectors is produced by such trademarks as: ExTech, Fielpiece, Testo etc.
Infrared detectors have an optical bench that the refrigerant passes through. The refrigerant absorbs IR radiation. The bench senses this and converts it into an alarm dependent on the amount of IR absorbed. The technology is very accurate and less prone to contamination. It has only been recently deployed in small hand held technology but has been widely used in larger fixed environmental detectors for many years. Check with manufacturer before using with HC’s. One of the best wellknown manufacturers of IR leak detectors is Bacharach.
Ultrasonic detectors work on sound waves emitted when gas or vacuum escapes through a small orifice (leak). The sound is well above the frequencies sensitive to the human ear. The electronics pick up these frequencies and amplify them into an audible output that we can hear. The technology isn’t new but has only recently become cheap enough to use in hand held leak detectors. The notable benefit of this type of detector is it will detect any gas or vacuum leak including nitrogen and HC refrigerants. Suitable for HC’s. This type of leak detectors is offered to you by AccuTrack, Reed Instruments, Wohler and other manufacturers
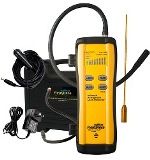
Residential Leak Protection: How To Choose The Right Leak Detection System
Wolseley PRO Pipeline Blog
Whether it is a slow leak from a plumbing fixture, or a catastrophic pipe failure, leaks can be destructive for a residence and extremely costly. We have all heard the stories of homeowners receiving extremely high water bills due to a flapper on a toilet starting to fail, or seeing disaster recovery companies at a residence due to a pipe or valve failure leading to major flooding. With todays technology, there are a myriad of ways to avoid leaks and detect them when they start, but which technology is the best?
How Do Leak Detectors Work?
In short, leak detectors will sense water flow in a building usually through a unit mounted on the incoming waterline. Messages can be sent out either via Wi-Fi or through a homes automation system. Ideally, the leak detection system will let you know if there is a small leak (showing water usage even if there should be no water flow at all). It will also shut the entire water system down if it detects a catastrophic failure such as a break in the main waterline.
What To Consider When Choosing A Leak Detection System
Important factors to consider when suggesting a leak detector for your customers are features, types of communication protocol, how the unit is powered, and whether the system will work if there is a breakdown in connectivity.
Automatic Water Shut-Off
While receiving a message about a leak in a residence is great, damage can be done between when the leak occurs and the time the homeowner receives the message. Automatic shut-off features will ensure that in the event of a catastrophic failure, the message is sent, but in the meantime, the system is shut down immediately.
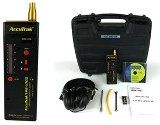
HOW TO SELECT THE CORRECT TYPE OF WATER LEAK DETECTION SENSOR FOR YOUR APPLICATION
Air Conditioning Drip Trays
Two sensors are available, the optical DTS sensor designed to sit in a drip tray, IP65 rated with no external electrical electrodes, and our leak detection cable type WDC4, this being very flexible, it can can be shaped around the tray for maximum coverage
Drip Trays underneath Water or Chilled Water Pipework
For long runs of drip trays our water detection cable type WDC4 is best suited as it can be serpentine in the tray to give maximum coverage.
Water or Chilled water Pipes with no Drip Tray
Our WDC4 detection cable can be fixed to the underside of the pipework along its entire length so any leak will be detected. Whilst care should be taken not to over tighten, cable ties can be used around the pipe at approximately 1 to 1.5 metre intervals
Service pits, Sump or Drain Pits
The best sensor for this application is our Optical spot probe. With no exposed electrical electrodes, this sensor is not susceptible to impact damage to the sensing part of it. Being IP65 rated, the sensor can be screwed to the inside of pit and fully submerged in water
Room perimeter monitoring and underfloor areas.
Two sensors are available, our standard WDC4 detection cable that will report a leak found anywhere along its length, and our DMWD cable, that when used with the DMWD alarm unit gives a measurement in metres from the controller to the leak. Both types of cable should be Clipped to the floor every 1 to 1.5 metres